Stage number | 3 stages or more | 4 | 5 | 6 | 7 | 8 | 9 1 |
Total number of production stopes | twenty three | 11 | 16 | 15 | 10 | 13 | 14 |
Average number of shots per auction | 0.4 | 0.5 | 1.2 | 2.1 | 2.1 | 2.7 | 3.36 |
Average per field loss /t | 63.3 | 77.0 | 81.2 | 179.1 | 282.5 | 2 | 344.6 |
Roof mining area accounts for the proportion of production stope /% | 26.1 | 36.4 | 62.5 | 10090 | 100 | 85.7 |
Indicator name | Value | Remarks |
Production capacity of ore block /t·d -1 | 75 | Average number from 1984 to 1986 |
Picking ratio /m·kt -1 | 14 | Average number from 1984 to 1986 |
Drilling station number / t · work class -1 | 47 | Average number from 1984 to 1986 |
Mining work efficiency / t · work class -1 | 10.13 | Average number from 1984 to 1986 |
Mine ore loss rate /% | 9.72 | Average number from 1983 to 1987 |
Mine ore depletion rate /% | 13.15 | Average number from 1983 to 1987 |
Explosive consumption / kg · t -1 | 0.5548 | Average number from 1984 to 1986 |
Pit wood consumption / m 3 · t -1 | 0.00169 | Average number from 1984 to 1986 |
Direct mining cost / yuan · t -1 | 9.14 | Average number from 1983 to 1987 |
Auto Gear Box Parts
1. Auto Gear Boxes Used for car parts, our gear box parts can use in BMW,Range Rover,Benz directly( TS 16949 Certified).
2. As customers' requirements, in perfect condition.
3. Aluminium casting, sand casting, die casting, gravity, low pressure die casting, high pressure die casting, casting foundry.
4. Applied software for specification drawings: Pro/E, Auto CAD, Solid work, CAXA UG, CAD/CAM/CAE.
5. Precision machining: CNC, milling machine, drilling machine, numerical lathe, all types of lathe.
6. Surface finish process: polishing, sand blasting, heat treatment, painting, powder coating, anodizing, electroplating, mirror polishing.
7. OEM&ODM service available.
8. Top quality and quick delivery time.
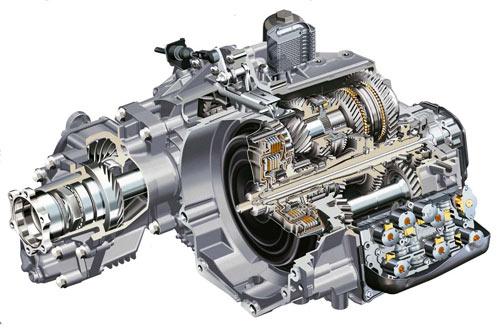
Auto Gear Boxes Advantage:
1. Size precision, smooth surface, high production efficiency.
2. Different surface treatments.
3. Advanced equipment, excellent R&D teams and strict quality control system.
We are the top manufacturers in Ningbo can supply OEM service for Auto Gear Boxes. Welcome to contact us!
Auto Gear Box Parts
Auto Gearbox,Die Casting Gear Boxes,Aluminum Auto Gear Box Parts,Aluminum Auto Gear Box Housing
Ningbo WEIBO Molding&Machine Co.,Ltd. , https://www.diecasting-manufacturers.com