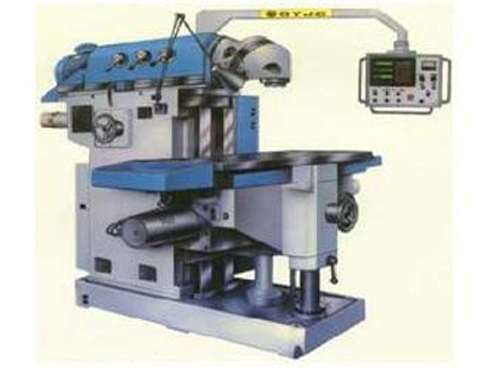
1. Pre-class maintenance
(1) Before driving, check whether the oil pools are short of oil, and use the clean oil to perform a refueling as shown in the lubricating chart.
(2) Check if the appearance and function of the power switch are good and the grounding device is complete.
(3) Check for looseness and loss of screws, eyes, handles, handballs, and cups, etc., of each component. If it is found, it should be tightened and filled in time.
(4) Check the drive belt condition.
(5) Check if the electrical safety device is good.
2. Class maintenance
(1) Observe the sensitivity, reliability, temperature rise, sound and vibration of motors and appliances.
(2) Check the sensitivity and reliability of the electrical safety equipment.
(3) Observe the temperature rise, sound direction and vibration of each transmission component.
(4) Check the working conditions of the plunger pump in the bed and the lift at all times. When the machine is running and there is no oil flowing out of the indicator, it should be repaired in time.
(5) Axial gaps in the longitudinal screw of the table and gaps in the drive were found and adjustments should be made as required.
(6) Spindle bearing adjustment.
(7) Adjustment of the quick-moving clutch on the table.
(8) Adjustment of the tightness of the drive belt.
3. After-class maintenance
After work, the equipment must be inspected and cleaned to perform routine maintenance work. The operating handles (switches) are placed in the neutral position (zero position) to open the power switch to achieve neat, clean, lubricated, and safe operation.
Regular maintenance
1. Every 3 months, the lubricating oil pool inside the bed, the inside of the lift platform and the base of the workbench, and the oil net for cleaning the lubricating oil pump with gasoline are not less than twice per year.
2. The lifting screw is lubricated once every two months with aluminum disulfide oil.
3. Adjustment of machine tool gaps:
(1) Adjustment of spindle lubrication must ensure that there is a drop of oil per minute.
(2) The adjustment of the longitudinal screw transmission gap of the table shall be adjusted every 3 months or adjusted according to the actual conditions of use. The requirement is that the transmission gap shall be fully reduced, the clearance of the screw shall not exceed 1/40 turn, and at the same time the full length There must be no jamming.
(3) The adjustment of the axial clearance of the longitudinal screw is to eliminate the transmission gap between the screw and the nut, and at the same time, to minimize the clearance between the axis of the screw and the table.
(4) The adjustment of the radial clearance of the main shaft bearing is adjusted according to the actual use conditions.
4. Adjustment requirements for quick-moving clutches on the table
(1) When the friction clutch is disengaged, the total clearance between the friction plates should not be less than 2 to 3 mm.
(2) When the friction clutch is closed, the friction plate should be tightly pressed and the core of the electromagnet should be fully tensioned. If the core of the electromagnet is properly mated, the electromagnet will not have a sound in the tensioned state.
On the basis of international cutting edge brush making technology and our own patented inventions, Haixing brush machines are stable and reliable and have been well accepted by the markets. By selecting different clamps and platforms, each Haixing brush machine can produce different types of brushes. Paint brush is one of the end products. These machines can produce flat paint brushes and rolling paint brushes. They have the functions of drilling holes and tufting filaments.
Paint Brush Making Machine, Paint Brush Machine
Yangzhou Haixing CNC Brush Machine Co., Ltd. , https://www.brushmachine.nl